Product Category
Instrumentation
Product
Digital Hour Meter
Application
Cement Mixers
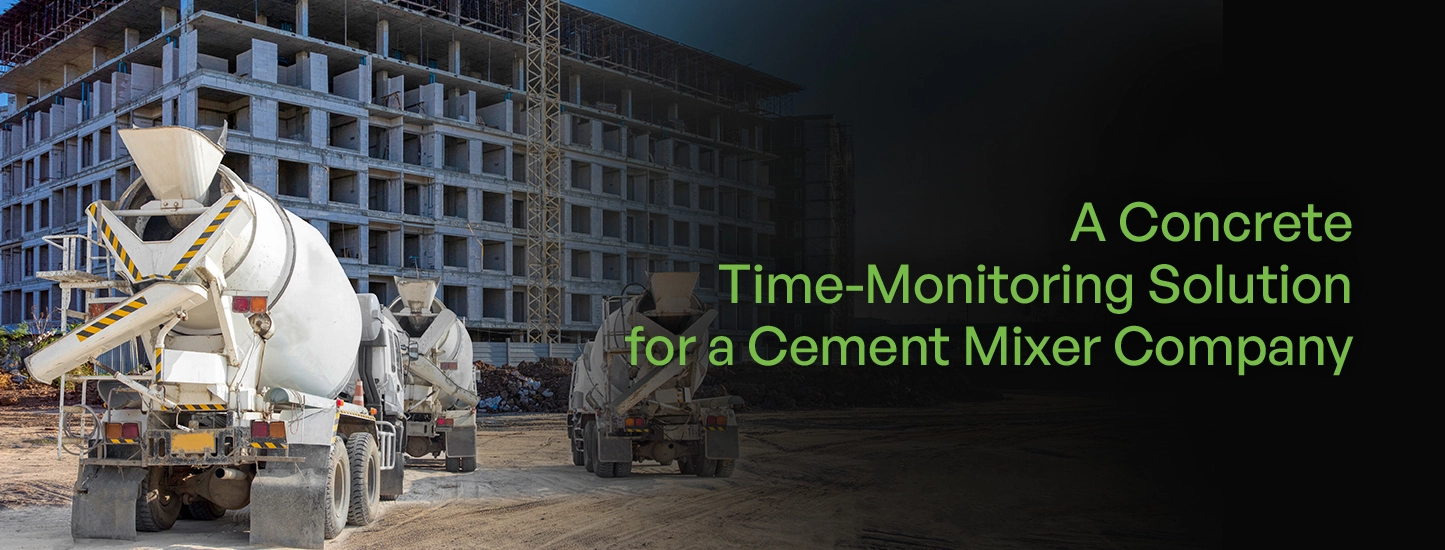
Monitoring and measuring the cement mixer’s operational hours for a construction equipment company.
Introduction
Concrete mixers make it simple to mix big volumes of concrete and cement. Concrete must be mixed thoroughly and fast in order to be effective, which is difficult to achieve by hand. Mixers are appropriate for a wide range of applications, from minor home repair projects to major commercial building projects. A certain client of ours that works in the construction equipment rental industry, was facing issues in monitoring the working time of their Cement Mixers. This case study is about how GIC Digital Hour Meter helped them navigate through their problem.
Challenges
The problem of inaccurately recorded machine operation hours is one that frequently plagues the equipment rental industry.
Predictive maintenance is required for these heavy-duty machines since they operate in harsh conditions for lengthy periods of time to avoid machinery breakdown.
It’s crucial to keep track of how many hours the equipment is used while renting it out to another user. For all of these reasons, precise time monitoring is very critical.
Solution
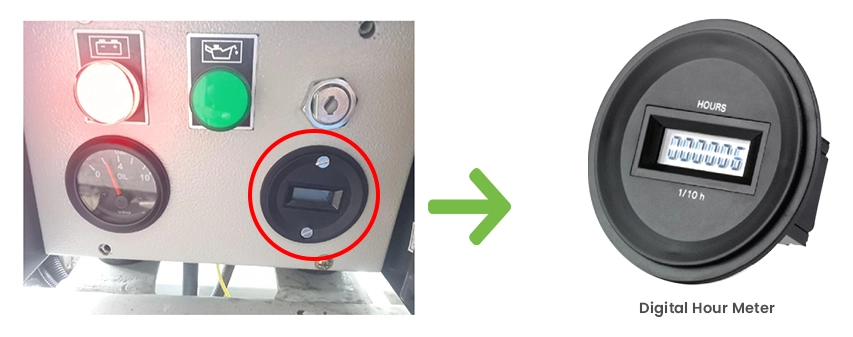
The GIC Digital Hour Meter brought the required precision and control in time measuring of the equipment. Using this, the client could plan the maintenance of the mixer as per the number of hours it was used for. In addition, the Digital Hour Meter provided the client with the exact number of hours the machinery was in use and could hence bill them accordingly. In addition, we installed one additional round plate on the backside of the device to protect it from vibrations that take place in harsh working environments. Earlier our client was using an hour meter of a different kind and make, and they were facing delivery issues.
The GIC Effect
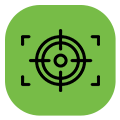
Accurate billing: By tracking the operational hours of rented equipment using the GIC Digital Hour Meter, the company can ensure accurate billing based on the actual usage. This helps prevent disputes and ensures fair charges for customers.
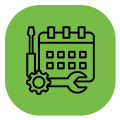
Maintenance scheduling: The hour meter provides real-time data on the equipment’s usage, allowing the company to schedule timely maintenance and service. This proactive approach helps prevent breakdowns, extends equipment lifespan, and enhances customer satisfaction.
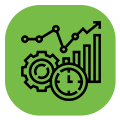
Efficient resource allocation: By monitoring the operational hours of each piece of equipment, the users can analyze usage patterns and optimize resource allocation. This enables them to make informed decisions regarding equipment availability, deployment, and replacements, ensuring quick delivery, maximum utilization and profitability.
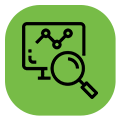
Monitoring contracts: A digital hour meter provides reliable data for monitoring contract terms and conditions. It helps track equipment usage within the agreed-upon timeframes, ensuring compliance and preventing any potential contract violations.
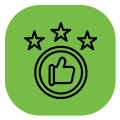
Withstands harsh environment: We installed the Digital Hour meter in such a way that the vibrations occurring during the usage in tough conditions, do not result in a breakdown or the hour meter registering a faulty reading.